In the world of construction and building design, managing moisture is one of the most critical factors in ensuring structural integrity, energy efficiency, and indoor comfort. Enter vapor barriers—a crucial yet often overlooked component in modern buildings. Vapor barriers are specially designed materials that play a vital role in controlling the movement of moisture within a structure. Whether it's protecting against mold growth, preventing damage to insulation, or reducing the risk of structural decay, these barriers are indispensable in creating a safe and durable indoor environment.
In this blog, we’ll dive deep into what vapor barriers are, how they work, and why they are an essential element of moisture management in both residential and commercial buildings.
Why Building Codes Matter for Vapor Barriers
Building codes are the backbone of safe and sustainable construction practices. These regulations are designed to ensure that every structure is built to be safe, durable, and energy-efficient, addressing key challenges like moisture control. In the context of vapor barriers, building codes play a vital role by defining how, where, and when these barriers should be installed to optimize performance and protect the integrity of the building.
The Role of Building Codes in Construction
The primary purpose of building codes is to set a standard that ensures buildings are constructed to protect the occupants and the environment. These codes serve several goals, all of which are critical for long-term sustainability. For example, safety is a primary concern, with codes designed to protect buildings and their occupants from hazards like moisture-related structural damage that could compromise the building’s stability.
Energy efficiency is another essential objective. Building codes enforce practices that conserve energy, such as using vapor barriers to maintain the effectiveness of insulation. This not only reduces heating and cooling costs but also contributes to environmental sustainability. Lastly, moisture control remains a core focus, as unchecked moisture can lead to wood rot, mold growth, and the deterioration of insulation, all of which can negatively impact the building’s performance and health.
How Vapor Barriers Fit into Building Code Requirements
When it comes to vapor barriers, building codes provide clear guidelines to ensure their effective use in controlling moisture. These regulations determine the placement, materials, and installation techniques to achieve optimal results. For instance, moisture protection is a key consideration. Codes specify where vapor barriers should be placed to prevent water vapor from seeping into walls, floors, and ceilings, which could lead to costly damage.
Energy efficiency is also a significant factor. By maintaining the integrity of insulation, vapor barriers contribute to meeting strict energy standards outlined in building codes. This ensures that the building retains its thermal performance over time. Compliance with these codes not only enhances the building’s functionality but also adds value by ensuring it meets industry benchmarks.
Key Building Codes That Regulate Vapor Barriers
Understanding the key building codes that regulate vapor barriers is essential for ensuring compliance in both residential and commercial construction. These codes establish standards for material use, placement, and performance, ensuring structures are safe, efficient, and durable. Vapor barrier regulations are embedded in major codes like the International Residential Code (IRC), the International Building Code (IBC), and energy codes such as ASHRAE and the International Energy Conservation Code (IECC).
International Residential Code (IRC)
The International Residential Code (IRC) is one of the most widely adopted building codes for residential construction in the United States and beyond. It sets clear guidelines for the use of vapor barriers in homes, ensuring proper moisture control while taking into account the unique challenges posed by different climate zones.
The IRC specifically considers climate zones, recognizing that vapor barrier requirements vary significantly based on environmental factors. For example, in colder climates, vapor barriers may be mandated to prevent warm indoor air from condensing within wall cavities, while in warmer climates, the rules may shift to avoid trapping moisture inside. Additionally, the IRC provides guidance on interior vs. exterior placement of vapor barriers. This ensures they are installed in a manner that prevents condensation and moisture buildup, protecting both the structure and the indoor air quality.
International Building Code (IBC)
For larger residential buildings and commercial structures, the International Building Code (IBC) serves as the governing standard. This code outlines specific requirements for vapor barriers that address the complexity of moisture control in large-scale constructions.
One key focus is moisture control in commercial buildings, which often face different environmental challenges compared to single-family homes. The IBC specifies the types of vapor barriers suitable for facilities like hospitals, schools, and office buildings, ensuring they are robust enough to handle high occupancy and diverse climate conditions. Furthermore, the IBC sets material standards, requiring vapor barriers to meet stringent criteria for performance and durability. This ensures long-term protection and compliance with building regulations.
Energy Codes (ASHRAE and IECC)
Energy codes such as ASHRAE 90.1 and the International Energy Conservation Code (IECC) emphasize the role of vapor barriers in achieving energy efficiency goals. These codes focus on reducing energy consumption through better insulation, sealing, and moisture management.
A critical element of these codes is the requirement for an effective thermal envelope. Vapor barriers contribute by preventing moisture-related issues that could compromise insulation performance, a core aspect of both ASHRAE and IECC standards. Additionally, these codes highlight the importance of insulation and air sealing, with vapor barriers working in tandem with other components to meet stringent energy efficiency benchmarks.
Climate Zones and Vapor Barrier Requirements
Climate plays a significant role in determining how vapor barriers are used within building construction. The placement, type, and effectiveness of vapor barriers are all influenced by the specific conditions of the climate zone where a building is located. Building codes account for these variations, ensuring moisture control strategies are tailored to meet the challenges posed by temperature and humidity levels.
Understanding Climate Zones
Climate zones are geographic regions defined by factors such as temperature, humidity, and seasonal variations. These zones help inform building practices, including the use of vapor barriers, to ensure structures are optimized for their environment.
Temperature is a key consideration. In cold climates, vapor barriers are designed to prevent warm indoor air from condensing within the building envelope, while in hot climates, they prevent outdoor heat and moisture from infiltrating. Humidity levels also play a critical role. High-humidity climates require more robust vapor barriers to protect against excessive moisture that can lead to mold growth, insulation damage, and structural decay. By tailoring vapor barrier requirements to specific climate conditions, building codes help protect both the structure and its occupants.
Vapor Barrier Requirements by Climate Zone
Building codes specify different vapor barrier requirements depending on the climate zone to ensure optimal moisture control. In cold climates, vapor barriers are typically installed on the interior (or warm side) of insulation. This placement prevents indoor moisture from reaching cold exterior walls, where it could condense and lead to issues like mold and structural damage.
In warm, humid climates, the requirements shift. Vapor barriers are often installed on the exterior side of the building envelope to prevent outdoor humidity from infiltrating and condensing within cooler interior spaces. This approach is essential for maintaining indoor air quality and preventing the degradation of insulation materials.
Mixed climates present unique challenges due to their varying conditions, with cold winters and humid summers. In these areas, codes may require vapor barriers to be used selectively, such as in roofs or basements, to address seasonal moisture concerns. Proper design and material choice are essential to ensure year-round performance in mixed climates.
Types of Vapor Barriers Recognized by Building Codes
Building codes recognize various types of vapor barriers, each suited to specific applications and climate conditions. These barriers are selected based on their permeability, durability, and ability to meet moisture control and energy efficiency standards. Understanding the key types of vapor barriers can help ensure compliance with building codes while optimizing the performance of a building’s envelope.
Polyethylene Sheeting
Polyethylene sheeting is one of the most commonly used vapor barriers in construction. Recognized by building codes for its reliability and cost-effectiveness, it is particularly favored in areas prone to high moisture levels.
As a Class I vapor barrier, polyethylene sheeting is highly impermeable, making it an ideal choice for high-moisture environments like crawlspaces and basements. Its ability to block almost all water vapor ensures long-term protection against moisture-related issues. Due to its versatility and availability, polyethylene sheeting meets the majority of building code requirements for both residential and commercial applications, cementing its widespread use across the industry.
Foil-Faced Vapor Barriers
Foil-faced vapor barriers offer a dual benefit of moisture control and improved energy efficiency, making them a popular choice for energy-conscious builders. These barriers reflect radiant heat while simultaneously blocking vapor transmission, creating a multifunctional layer within the building envelope.
Their dual purpose is particularly beneficial in energy-efficient buildings, as they enhance both the thermal envelope and moisture management. Building codes often recognize foil-faced barriers for their performance in hot climates, where they are frequently installed in attics and exterior walls. By addressing both radiant heat and humidity, they effectively meet building code standards in warm, sunny regions.
Liquid-Applied Vapor Barriers
Liquid-applied vapor barriers are gaining popularity for their seamless and adaptable application, especially in commercial projects. These barriers are applied directly to surfaces as a liquid, creating a continuous and durable moisture-resistant layer as they cure.
Their versatility is unmatched, allowing them to be used on irregular surfaces and around complex penetrations such as pipes, ducts, or windows. This makes them particularly useful in areas where traditional sheet or roll vapor barriers may be impractical. Additionally, liquid-applied barriers meet building code requirements for durability and long-term moisture control, making them an excellent choice for demanding applications, such as large commercial buildings or structures in challenging climates.
Installation Best Practices to Meet Building Code Requirements
Proper installation of vapor barriers is crucial not only for ensuring effective moisture control but also for meeting the specific requirements outlined in building codes. Adhering to these best practices helps prevent issues like condensation, mold growth, and energy inefficiencies, ensuring the long-term performance of the building envelope.
Proper Placement of Vapor Barriers
The placement of vapor barriers plays a critical role in moisture management and is heavily influenced by climate zone requirements. Building codes provide clear guidance on where vapor barriers should be installed to optimize their effectiveness.
For instance, interior or exterior placement depends on the climate. In cold climates, vapor barriers are typically installed on the interior (warm side) of walls to prevent indoor moisture from reaching cold exterior surfaces. Conversely, in warm climates, they are installed on the exterior to block outdoor humidity from infiltrating. Regardless of placement, full coverage is essential. This means ensuring that vapor barriers extend across all required surfaces, including walls, floors, and ceilings, with special attention given to areas around penetrations like pipes and wiring.
Sealing Joints and Penetrations
Proper sealing is another critical requirement for vapor barrier installation. Building codes often emphasize the importance of airtightness to prevent moisture from bypassing the barrier.
To meet these requirements, it is essential to use vapor barrier tape to seal all seams and edges. This ensures a continuous, airtight layer that conforms to code standards. Around openings like electrical outlets, plumbing, and HVAC ducts, additional measures such as caulk or expanding foam should be used to seal gaps effectively. This prevents moisture from entering through otherwise overlooked areas, enhancing the overall performance of the barrier.
Avoiding Common Installation Mistakes
Even minor errors during installation can lead to significant problems and potential code violations. Recognizing and avoiding these common mistakes is key to a successful installation.
One common error is incorrect placement of the vapor barrier. Installing it on the wrong side of insulation, such as placing it on the warm side in a hot climate, can lead to condensation and moisture accumulation. Another frequent issue is inadequate sealing. Gaps in seams, edges, or around penetrations can compromise the barrier’s effectiveness and result in moisture damage. Finally, using a vapor barrier with an improper thickness—one that does not meet the required permeability rating for the specific climate zone—can result in noncompliance with building codes and insufficient moisture control.
FAQs
Contact Trench Guys Today!
Trench Guys will do everything we can to ensure your experience with us is excellent.
Request A FREE Estimate
Request a Free Estimate Form
Checkout Recent Post
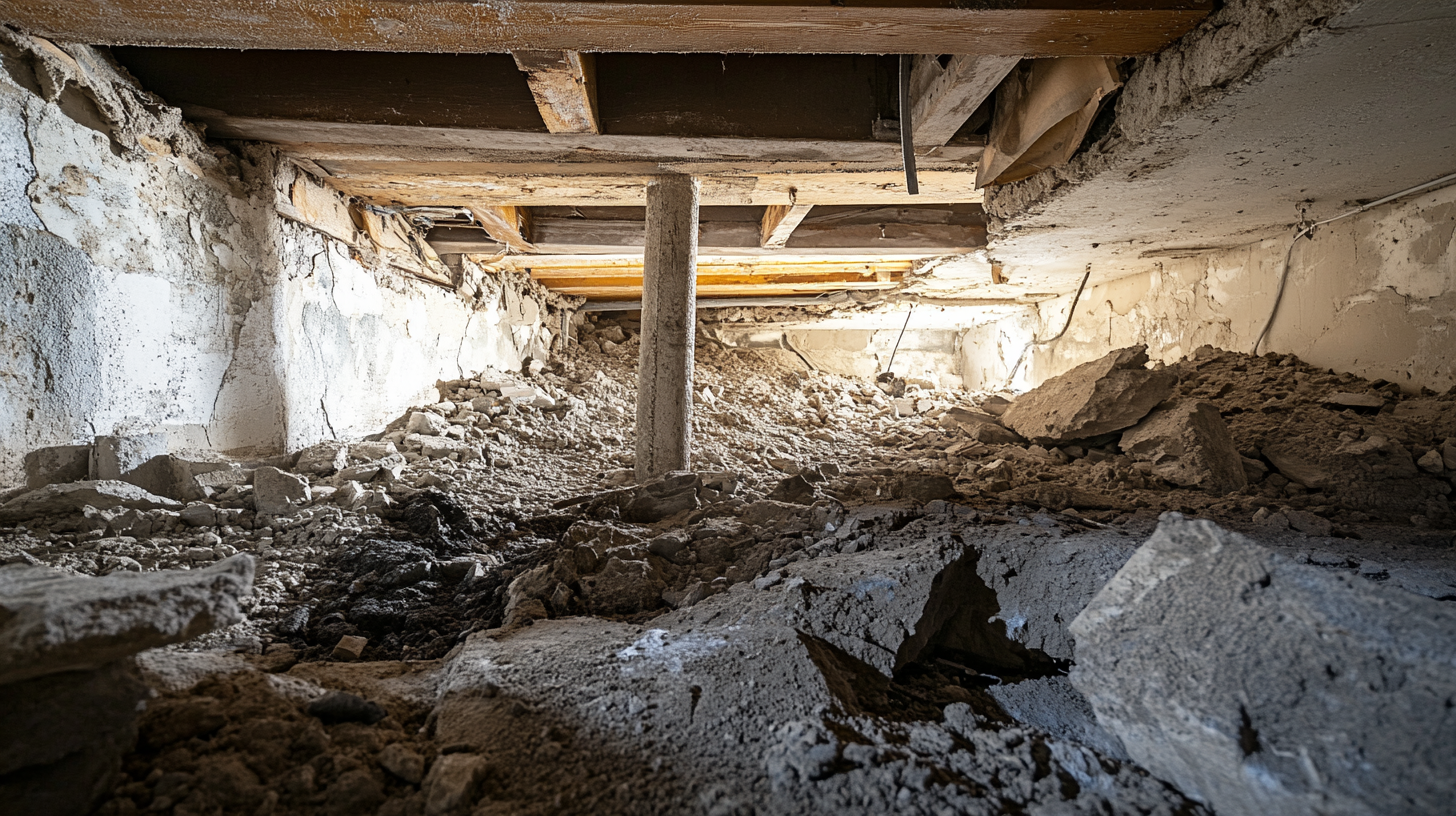
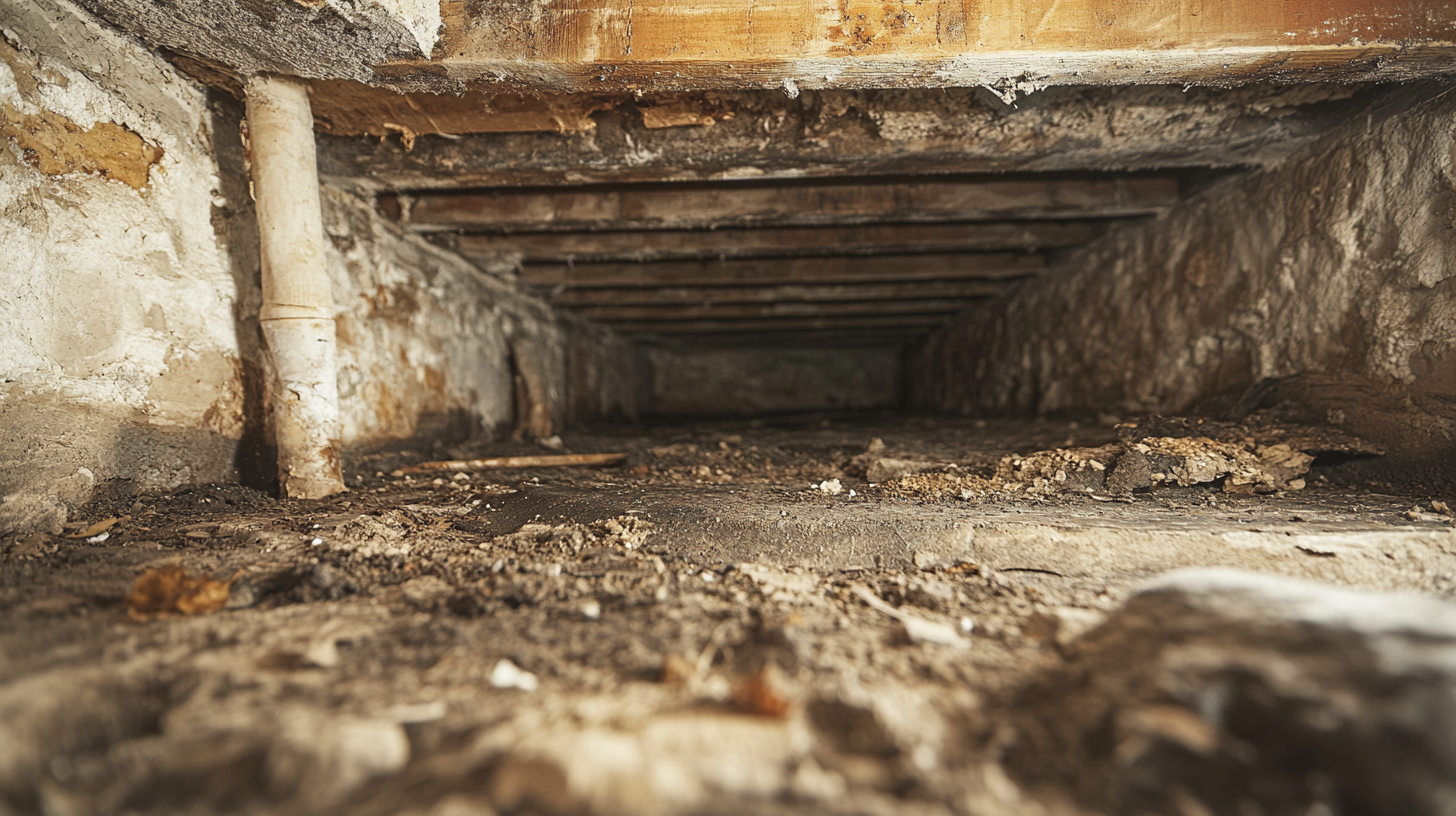
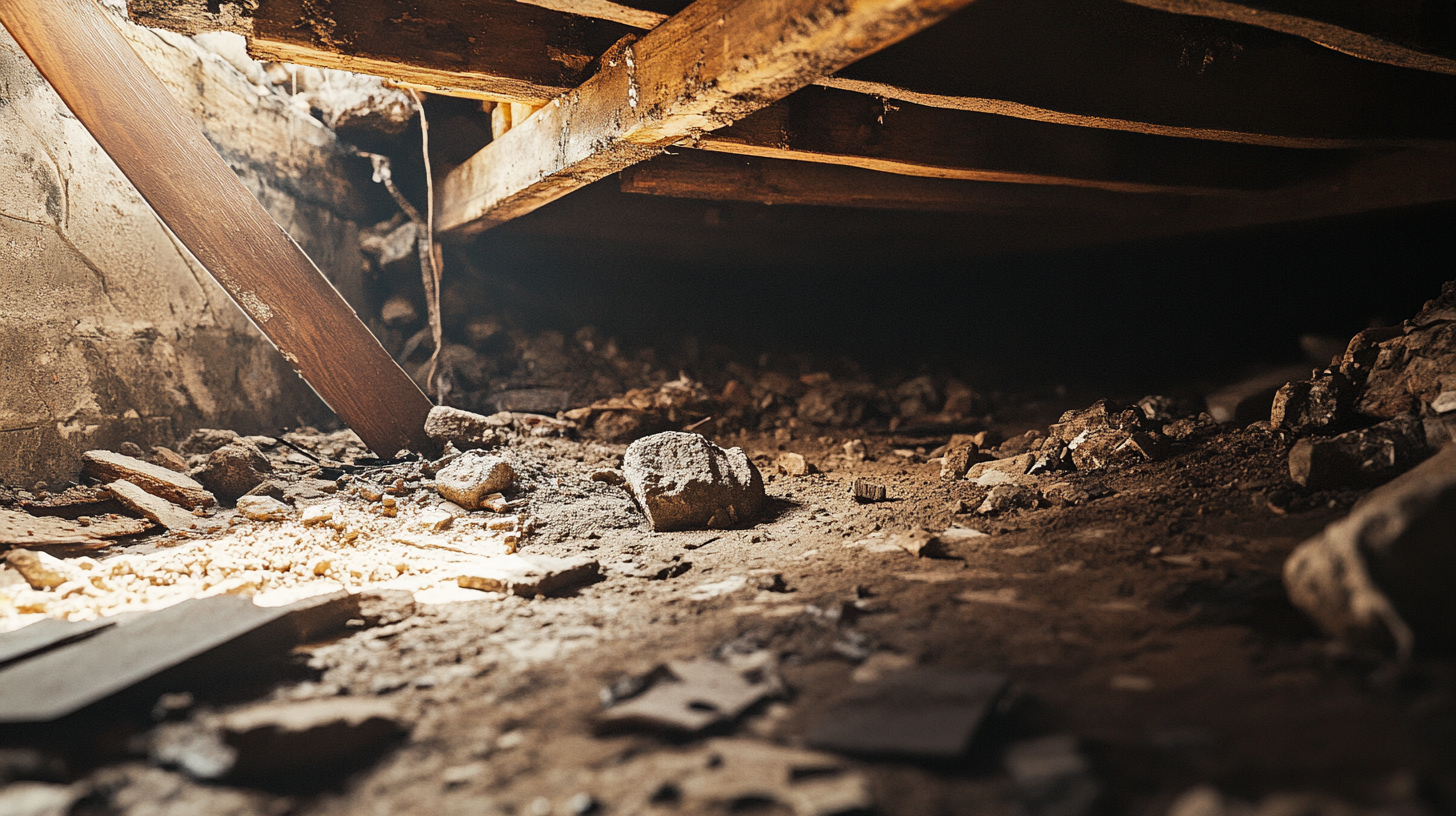
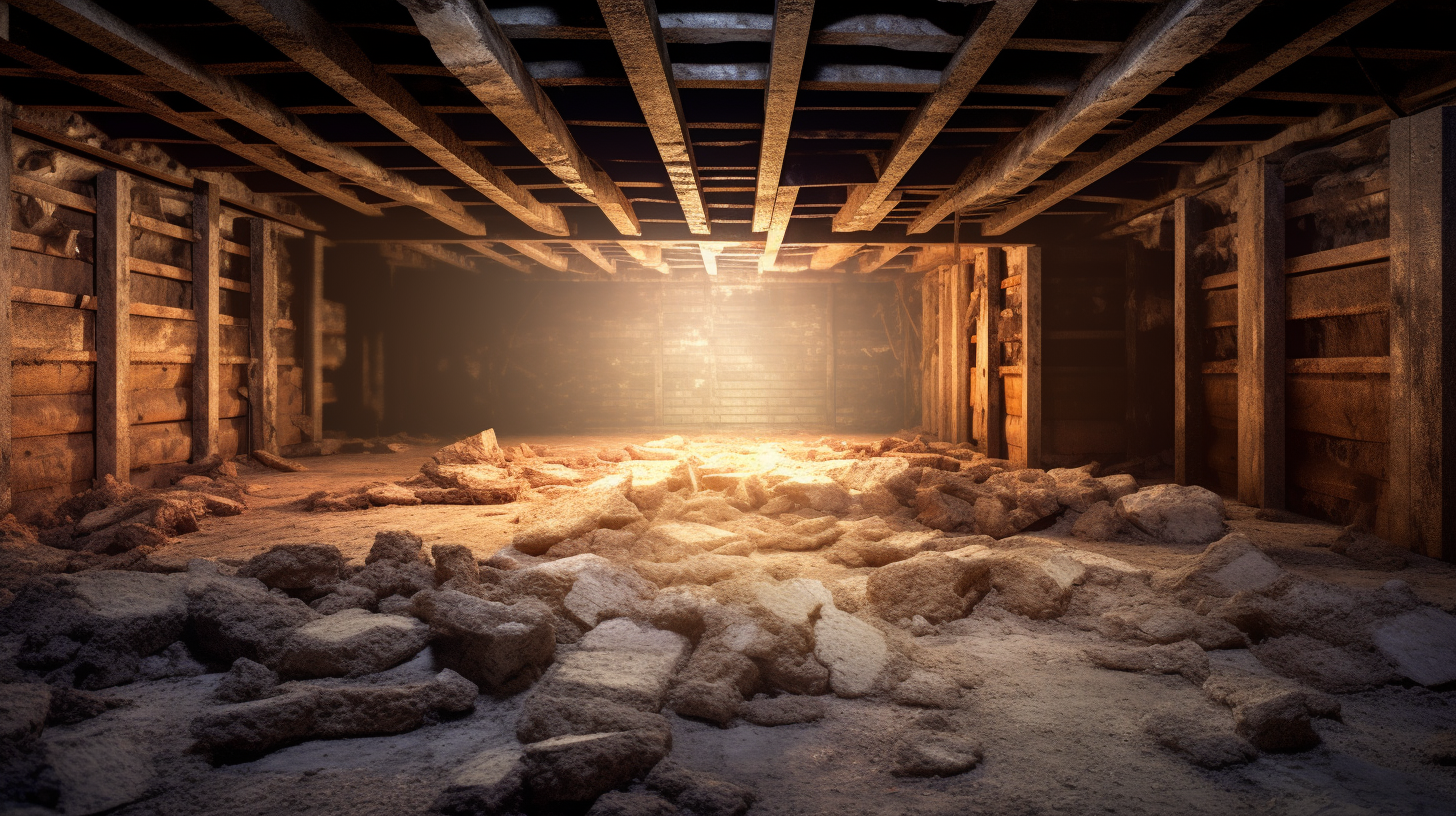
Got a Question? We’re Here to Help.
You can arrange an appointment or make an enquiry by phone or email, orget in touch to us via our contact form.